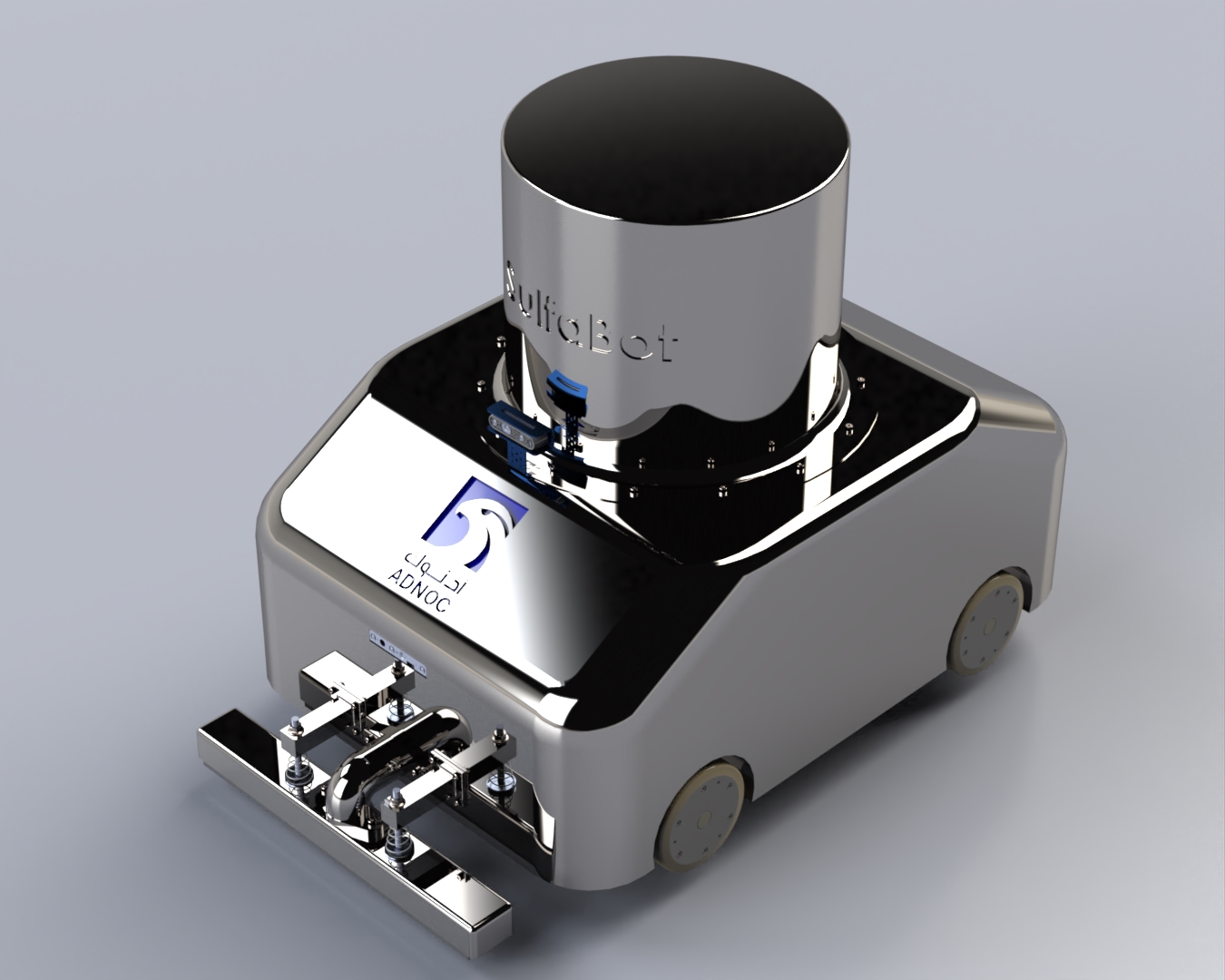
The robot demonstrates the feasibility of cleaning granulated sulfur and sulfur dust (300 μm or less) within main storage facilities, with an existing IECEx/ATEX-rated stand-alone machine, with a customized vacuum system (also safety-rated ).
Safety and functionality:
- The system meets the requirements of dust zones 20, 21 and 22.
- The system meets Class 4 (Class T) temperature requirements: 135°C.
- System meets requirements to safely absorb and retain sulfur dust and coarse granules, and prevent potential flammability at 160-190°C
- The main device meets IECEx/ATEX explosion-proof certifications.
- The proposed system probably uses a specific, custom-made anti-static/explosion-proof vacuum cleaner, appropriately rated for the environment.
- The proposed system will operate successfully in an environment of ~60°C
Autonomous and innovative building cleaning. Through a scale platform of buildings and walls equipped with modular cleaning units. Being an innovative and unique robot in its style, it offers its clients a quality service, with qualified and efficient treatment.
There is no risk to human life, exposing yourself to the dangers of working conditions when cleaning large buildings.
It was decided to do it autonomously and applying physical laws instead of using built-in guide rails or winch systems.
The proposed platform adopts a high vacuum system to scale the surface efficiently and safely, maintaining good contact with various types of surfaces with propellers and generators, with an optimal design to ensure an absorption force greater than that necessary per propeller.
The high friction dry type vertical surface cleaning unit is designed efficiently, autonomously and economically, and its operating conditions are examined by modern methods to remove more than 88.9% of contaminants on a glass.
Safety and functionality:
It has an accelerometer that, as a safety feature, when detecting that the device is descending at high speeds at the programmed speeds, opens a parachute to protect people, buildings, equipment and other things.
- Capable of detecting obstacles and stopping to avoid any collision.
- Have an emergency stop button.
- Can be deployed on demand with limited setup time.
- Fixing adapted to the shape of the façade improves safety.
- The robot moves safely: improved mobility.
- The robot vacuums complex parts of the surface: improved stability.
- Cleaning power of 525.5 m2/h: high efficiency.
- Immediate control of movements.
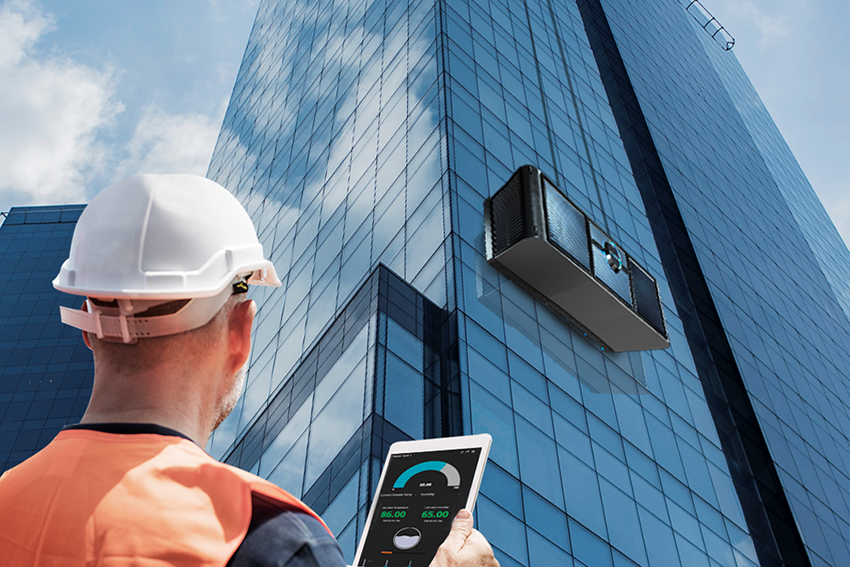
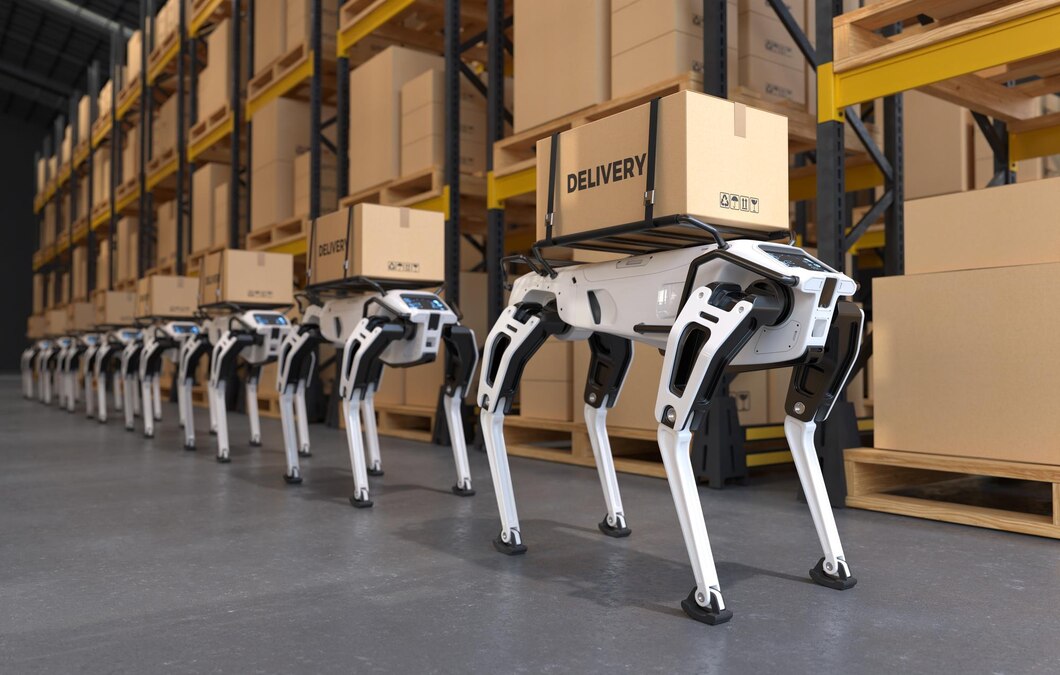
Increase efficiency: Automating a warehouse can help streamline operations and make them more efficient by reducing errors, increasing speed, and optimizing workflows.
- Improve accuracy: Automated systems can help eliminate errors and improve accuracy in tasks such as inventory management, order fulfilment, and shipping.
- Reduce labour costs: By automating repetitive or labour-intensive tasks, companies can reduce their reliance on human labour and potentially reduce labour costs.
- Increase capacity: Automated systems can allow a warehouse to handle more inventory and process more orders, which can help increase overall capacity and throughput.
- Enhance safety: Automated systems can help improve safety by reducing the need for workers to perform hazardous tasks such as heavy lifting or working at heights.
- Improve customer service: By improving efficiency and accuracy, companies can provide faster and more reliable service to their customers, leading to increased customer satisfaction and loyalty.